Anforderungen an den Modellantrieb
|
1. Einleitung
|
Als Modellantrieb kam für mich nur ein Gleichstrom-Elektromotor in Frage, da im
Betrieb leise und geruchlos sowie einfach in Drehzahl und Drehrichtung zu regeln. Dank den heutzutage erhältlichen Akkus und Ladetechniken liegen auch längere Fahr- respektive Betriebszeiten mit relativ kurzen Ladezeiten drin und das Modell
kann zudem problemlos in geschlossenen Räumen betrieben werden.
Über die Berechnung oder Entscheidungskriterien für die Wahl eines geeigneten Elektromotors (EMotors) finden sich
eine Vielzahl von Informationen in Internetforen oder gar Modellbaumagazinen, welche den Leser
oft mit einer gewissen Ratlosigkeit, Verwirrung oder gar falschen Informationen zurücklässt.
Mein Ziel war, die Anforderungen (benötigtes Drehmoment und Drehzahl) an einen geeigneten Elektromotor als konkrete Zahlenwerte vorliegend zu haben.
Beispielweise sind "Hohe Leistung" oder "möglichst kräftig" keine klaren Anforderungen.
Hingegen sind Anforderungen wie "mindestens ein Drehmoment von 10 Newtonzentimeter [Ncm]" oder "Drehzahl von midestens 4000 Umdrehungen pro Minute [1/min]" klar und unmissverständlich.
Wie man zu solchen konkreten Anforderungen kommt, ist Inhalt dieses Kapitels.
Auf dieser Basis war/ist es möglich, anhand von Herstellerinformationen ein(en) potentielle(n) EMotor(en) in die engere Wahl einzubeziehen.
Vor der Entscheidung sollte unbedingt noch die Getriebeberechnung- und auslegung erfolgen. Durch Einbezug der berechneten Drehmomente
können allfällige Schwachstellen (z.B. Überlastung einzelner Zahnräder und vor
allem von Wellenverbindungen) mit diesem Schritt (gratis!) feststellen. Erst dann sollte der EMotor angeschafft werden.
|
2. Allgemeine Anforderungen an den Modellantrieb
|
Bevor man anfängt Kataloge zu wälzen oder in Internetforen um Hilfe zu rufen, sollte man sich ein paar Solldaten notieren.
Dies vereinfacht oder zumindest strukturiert die eigene Recherche und gibt Anderen die Möglichkeit, sinnvolle Antworten auf etwaige Hilferufe zu geben.
Dazu zählen:
- Gewicht des Modellfahrzeuges (leer und ev. beladen)
- gewünschte Geschwindigkeiten des Modells (Einsatz eines Schaltgetriebes ja/nein?)
- gewünschtes Einsatzgebiet des Modells (benötigtes Drehmoment?)
- Reifen-Aussendurchmesser (beeinflusst benötigtes Drehmoment und gewünschte Geschwindkeit)
- optional die gewünschte Akkuspannung (ev. hat man bereits ein paar Akkus oder Drehzahlsteller rumliegen)
Auch wenn das Modell erst als Papierzeichnung existiert, so kann man beispielsweise das Gewicht abschätzen, indem man Gewichtsangaben von ähnlichen,
bereits existierenden Modellen verwendet, oder schlicht ein Zielgewicht annimmt.
Zielgewichte machen speziell bei Modell-Nutzfahrzeugen Sinn, welche aufgrund ihres Einsatzgebietes
eine gewisse Masse auf den Boden bringen müssen (Stichwort Reifenhaftung!), beispielweise Radlader, Dumper oder dergleichen um nicht bereits bei einem lose aufgeschütetetn Sandhaufen zu kapitulieren.
Obwohl Masse zu beschleunigen Energie kostet (aus dem Akku), tritt dieser Umstand ob des entgangegen Spielspasses in den Hintergrund.
Zudem sind Beschleunigungsphasen eher kurz und die Endgeschwindigkeiten gering, sodass dieser Umstand nicht sehr ins Gewicht fällt.
|
2.1 Allgemeine Wunschanforderungen
|
Die Anforderungen an den Modellantrieb sollte man sich erstmal stichwortartig notieren. Meine persönliche Wunschanforderungen an den Antrieb meines Unimogs
lauteten:
- die maximale Geschwindigkeit soll Schritttempo betragen (ca. 5km/h)
- Eine Akkuladung sollte mindestens 1 Stunde Betrieb ermöglichen (oder: Der Stromverbrauch sollte möglichst gering sein)
- möglichst kraftvolles und dynamisches Fahrverhalten in den unterschiedlichen Fahrsituationen (siehe Kapitel 2.2)
- Antriebsmotor und weitere Elektronik-Komponenten (Bsp. Akku, Drehzahlsteller) sollten von Aussen nicht sichtbar sein
- Kernelemente des Vorbild-Antriebsstranges wie Allradantrieb, Portalachsen und Schubrohre sollten auch beim Modell umgesetzt werden
|
2.2 Gewünschte Einsatzgebiete / Fahrsituationen:
|
Das gewünschte Einsatzgebiet, respektive die gewünschten Fahrsituationen, welche das Modell meistern sollte sind elementar wichtig für die Auslegung eines geeigneten EMotors. Als Beispiel mögen folgende Vergleiche dienen:
Beispiel 1: Motorisierung eines Modell-Gabelstaplers und eines Modell-Radladers.
Beiden Modellen gemeinsam ist, dass sie sehr oft Beschleunigen, Abbremsen und die Richtung kehren.
Der Gabelstapler wird auf ebenem Untergrund betrieben und muss grundsätzlich nur sein Eigengewicht plus dasjenige der Ladung bewegen, wohingegen der Radlader seine Antriebskraft dazu nutzen muss, die Ladeschaufel ins Erdreich zu treiben.
Beispiel 2:Motorisierung zweier Modell-Traktoren
Der Eine Modelltraktor soll die Funktionen des Vorbilds im lockeren Erdreich (Bsp. Sand) ausüben können. Der Zweite Modelltraktor soll im heimischen Garten einen Pflug durch gewachsenen Mutterboden ziehen können.
Letzter Modelltraktor wird nicht nur eine wesentlich grösser dimensionerten EMotor benötigen, sondern auch erheblich stabilder gefertigt sein müssen und zudem ein Eigengewicht von über 60kg benötigen, um die Kraft überhaupt auf den Boden übertragen zu können.
Zurück zu meinem Unimog-Modell: Für den Einsatz meines Unimogs sah ich zwei unterschiedliche Einsatzgebiete vor, nämlich Befahren ebener Flächen (Rasen, Pflaster, etc.) und grosser Steigungen/ Gefälle (Waldboden,
ausgefahrene Feldwege, etc.). Mein Modell sollte zudem auch noch mit 10 Kilogramm Gewicht beladen noch flott unterwegs sein und zusätzlich auch mindestens einen Einachs-Anhänger durch das Gelände ziehen können.
Die Frage nach der Anzahl Geschwindigkeitsstufen (braucht es dazu ein Getriebe?) habe ich beantwortet, indem ich mir diejenigen Modelleinsätze mit den ungefähr gewünschten Modellgeschwindigkeiten aufgelistet habe, welche ich als "spielenswert" erachte:
- 1) Schneeschleudern/ -fräsen (5 cm/s)
- 2) Rasenmähen/ Schneepflügen (30cm/s)
- 3) Ladung von A nach B transportieren (50cm/s)
- 4) Schnellgang in Schrittgeschwindigkeit von ca. 5km/h (120cm/s)
Bereits an dieser Stelle wird klar, dass zur Erzielung dieser verschiedenen Geschwindigkeiten (ohne den EMotor zu überlasten) der Einsatz eines Getriebes mit unterschieddlichen Übersetzungen notwendig wird.
Die am einfachsten zu realisierende Variante eines Modellantriebes ist sicherlich auf ein Schaltgetriebe gänzlich zu verzichten und stattdessen eine feste Übersetzungsstufe einzubauen - beispielweise beim oben aufgeführten Beispiels mit dem Modell-Gabelstapler.
Der Einsatz eines mehrstufigen Getriebes hat den Zweck, das Drehmoment des noch zu bestimmenden Elektromotors an die jeweilige Fahrsituation anzupassen (Bsp. Bergfahrt im Gelände) und somit haushälterisch mit der mitgeführten Energie umgehen.
Wie dieses Getriebe auszusehen hat, ist im separaten Kapitel GETRIEBEPLANUNG beschrieben.
| |
3. Anforderungen in Zahlen
|
Wie Eingangs erwähnt, kann mit den allgemeinen Anforderungen, welche qualitativen Charakter haben, noch kein EMotor ausgewählt werden.
Dieses Unterkapitel hat das Ziel, quantitative Anforderungen zu definieren.
Dazu wird versucht, die benötigte
Antriebsleistung für das zukünftige Modell abzuschätzen
unter der Prämisse, sämtliche Fahrsituationen bei geringstem Energieverbrauch zu bewältigen.
Für die Abschätzung der benötigten Antriebsleistung habe ich zwei
verschiedene Methoden angewandt:
- Variante 1: Berechnung nach der im Fahrzeugmodellbau gebräuchlichen
"Massstabsformel"
- Variante 2: Berechnung nach der "Drehmomentmethode" (Abschätzung der
Antriebsleistung unter Verwendung von berechneten Drehmomenten an den
Antriebsrädern)
Die Idee hinter der Verwendung beider Varianten
ist die Abhängigkeiten von Drehmomenten, Antriebsleistungen und
Getriebeübersetzungen besser verstehen zu könnnen und die Ergebnisse
miteinander zu vergleichen um eine Aussage über die Zweckmässigkeit der
einfachen "Massstabsmethode" anstellen zu können.
|
3.1 Variante A: Berechnung nach der "Massstabsformel"
|
HINWEIS:
Diese Näherungsformel sollte ausschliesslich für Lastwagen- oder Auto-Modellfahrzeuge, nicht für Nutzfahrzeugmodelle wie
Radlader, Dumper, Traktoren oder kettengetriebene Fahrzeuge angewendet werden.
|
Die im Fahrzeugmodellbau oft angewandte Methode zur Bestimmung der
benötigten Antriebsleistung basiert auf einer einfachen Näherungsformel
und lautet:
P_Modell = (Leistung des Originals [Watt] :
Massstab^4 ) * Korrekturfaktor
Der Korrekturfaktor wird verwendet, um Verluste im Antriebsstrang und
Elektromotor zu kompensieren. Gebräuchlich ist ein Korrekturfaktor
mit dem Wert 2.
Das Vorbild hat gemäss Herstellerangaben eine Antriebsleistung von
157kW. Die benötigte Antriebsleistung für mein Modell im Massstab 1:8
berechnet sich somit wie folgt:
P_Modell = (157'000W : 8^4) * 2 =
(157'000:4096)*2 = 72W
Um dieses Ergebniss mit demjenigen der nachfolgenden Berechnungsvariante vergleichen zu können, dient folgende Tabelle,
welche aufzeigt, welchem Drehmoment bei welcher Drehzahl diese berechneten 72 Watt entsprechen. Dazu lässt sich die einfache
Näherungsformel
M = P / (n * 0.1)
nutzen und die Drehzahlen beispielweise in
Stufensprüngen von 2'000 1/min innerhalb eines Drehzahlbereiches, in denen viele der handelsüblichen EMotoren für unsere Zwecke liegen (vgl. auch Kapitel 'AUSWAHL EMOTOR', Abschnitt 5).
Leistung [W] |
Drehzahl [1/min] |
Drehmoment [Ncm] am EMotor-Abtrieb |
72 |
2'000 |
36 |
72 |
3'000 |
24 |
72 |
4'000 |
18 |
72 |
5'000 |
14.4 |
72 |
6'000 |
12 |
72 |
8'000 |
9 |
72 |
10'000 |
7.2 |
72 |
12'000 |
6 |
Tabelle 1: Benötigtes EMotor-Drehmoment nach Massstabsmethode
Lesebeispiel: Eine Leistung von 72 Watt am Abtrieb des EMotors stellt sich ein bei einer Drehzahl von 6'000 1/min
(Umdrehungen pro Minute) und einem Drehmoment von 12 Ncm (Newtonzentimeter).
Diese Angaben finden sich typischerweise in den Datenblättern der EMotor-Hersteller.
Nachfolgend der zweite Versuch zur Berechnung des benötigten Drehmomentes und Drehzahl mit der "Drehmomentmethode".
|
3.2 Variante B: Berechnung nach der "Drehmomentmethode"
|
Bei dieser Methode wird versucht zu ermitteln, welches Drehmoment am
Radabtrieb resp. den Radnaben erforderlich ist um die geforderten
Fahrleistungen zu erzielen.
Um das Gewicht meines zukünftigen Modells abschätzen zu können,
habe ich ein paar Komponenten und Rohmaterialien auf die Waagschale gelegt,
respektive aus Katalogen rausgesucht. Dies waren unter anderem: Akkus
(ca.2kg), Reifen und Felgen (ca.3kg), Antriebsteile aus Alu/Stahl (ca.3kg), Aufbauten
(ca.1kg), Verschraubungen und Kleinteile (ca 1kg.), Fernsteuerungskomponenten
(ca.0,5kg) und Hydraulikkomponenten (ca.2,5kg) ergeben ein
(geschätztes) Betriebsgewicht von ca.13kg. Spätere An- oder Aufbauteile
(Bsp. Hydraulikkran, Scheepflug, etc.) schätze ich auf maximal 5kg.
Der Motor muss also zwischen 15-18kg Gewicht beschleunigen, respektive
vier Räder, welche mit diesem Gewicht belastet sind aus dem Dreck bewegen.
Für sämtliche, nachfolgenden Berechnungen wird von einem Fahrzeuggewicht
von m=18kg, respektive von einer Gewichtskraft von F_g = m * g = 18kg
* 9.81 m/s2 = 180N ausgegangen. Der Reifendurchmesser war mit d=156mm
gegeben (Geländereifen Fa. Conrad / Schink).
Nun galt es abzuschätzen, wie gross die notwendigen Drehmomente an den
Rädern (=an den Achsabtrieben) in unterschiedlichen Fahrsituationen sein
müssen.
Auf ebener Fläche und hartem Untergrund ist ein geringeres Drehmoment
erforderlich, als bei Geländefahrten. Für die Abschätzungen
habe ich drei Fahrsituationen ausgewählt, die auch beim Fahrrad-
oder Autofahren kritsch sind. Zusätzlich habe ich noch - als Vergleich -
das benötigte Drehmoment beim Fahren auf ebener Fläche (Bsp. Asphalt)
berechnet:
(1) Überfahren einer hohen Schwelle
(2) Überfahren von feuchtem Erdreich (Räder sinken ein)
(3) Überfahren einer ebenen Fläche
(4) Überfahren einer Steigung (Bsp. Rampe)
|
|
3.2.1. Überfahren einer Schwelle
|
Im Gegensatz zum Fahren / Beschleunigen auf ebener
Fläche, wo lediglich die sog. 'Massenträgheit' überwunden werden muss
(Reibung, Walkwiderstände der Reifen etc. erstmal ausgenommen), erfordert
das Überfahren einer Schwelle, dass ein Teil des Fahrzeuggewichtes in die
Höhe gestemmt werden muss. Dieser "Teil" ist abhängig von der Höhe der
Schwelle, also dem resultierenden Winkel α : Je höher die Schwelle (Winkel
α wird grösser), umso mehr spielt das Fahrzeuggewicht eine Rolle.
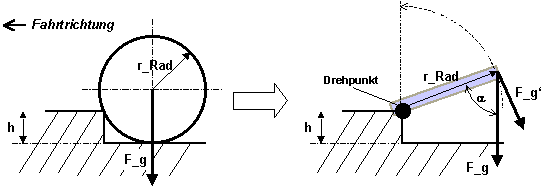
Bild 1: Überfahren einer Schwelle
Verdeutlicht ist dies in der rechten Darstellung in Bild 1: Ein Hebelarm der Länge
'r' der am "Drehpunkt" der Schwellenkante mit der Höhe 'h' "befestigt"
ist.
Annahme für das Beispiel: Bei einer Höhe h der Schwelle von r/2 und
der Gewichtskraft F_g von 45N (=180N/4 für ein Rad) ergibt sich:
cos(α) = (r/2) / r = 1/2 = 0.5 --> Winkel
α = 60°
F_g' = cos(90°-α) * F_g = cos (30°) * 45N =
39N
Die Kraft F_r muss demzufolge grösser als die Kraft F_g' von 39N sein,
um das Hindernis zu überwinden. Für das benötigte Drehmoment an
einem Radabtrieb gilt:
(1) M_Rad_Schwelle = F_g' * r_Rad =
39N * 0.0785m = 3.06Nm
Das Drehmoment am Radabtrieb muss folglich grösser als 3.06Nm sein, um
eine Schwelle mit der Höhe von 38mm zu überwinden. Würden alle vier Räder
gleichzeitig an einer solchen Schwelle anstehen, muss das Resultat noch
mit 4 multipliziert werden. Steht nur ein Rad an einer solchen Schwelle,
schieben die drei restlichen Räder je nach Untergrund (Haftreibung) mehr
oder weniger unterstützend mit, die Schwelle erfolgreich zu überwinden.
Diejenigen Leser welche mit Ihrem Auto einen "Laternenparkplatz" auf dem
Bürgersteig in der Stadt benutzen dürfen, kennen diesen Umstand sicherlich
auch aus der Praxis.
|
3.2.2. Überfahren von feuchtem Erdreich
|
Gemäss physikalischem Gesetz hängt die sog. 'Haftreibungskraft' nicht
von der Grösse der Auflagefäche (den Teil des Reifenumfanges unter dem
Winkel α)wie in Bild 2 dargestellt ab, sondern ist proportional zur Normalkraft F_g.
Bild 2: Überfahren von feuchtem Erdreich
Der
Proportionalitätsfaktor wird Haftreibungszahl µ' genannt. Nicht zu
verwechseln mit der sog. 'Gleitreibungszahl' µ (ohne Strich'). Die
Haftreibung ist entscheidend, dass z.B. das Fahrzeug auf der Strasse
haftet (Neudeutsch: "Grip"), wobei die Gleitreibung entweder stört (Bsp.
Wellenlager) oder nützt (Bsp. Bremse). Die sogenannte Rollreibung µ_r ist für die angestellten Abschätzungen nebensächlich.
Eine Übersicht einiger Haftreibungs- Gleitreibungs- und Rollreibungszahlen:
Haft-und Gleitreibung |
Haftreibungszahlen µ' |
Gleitreibungszahlen µ |
|
trocken |
geschmiert |
trocken |
geschmiert |
Stahl auf Stahl |
0.15 |
0.12...0.11 |
0.09...0.03 |
0.009 |
Stahl auf Holz |
0.6...0.5 |
0.1 |
0.5...0.2 |
0.08...0.02 |
Stahl auf Eis |
0.027 |
0.014 |
Gummi auf Asphalt |
0.9 |
0.85 |
0.45 (nass) |
Gummi auf Eis |
|
0.15 |
Tabelle 2: Haft- und Gleitreibungszahlen (Quelle: Dobrinski
et al, Lit [10])
Rollreibung |
Rollreibungszahlen µ_r |
Auto auf Asphaltstrasse |
0.025 |
Auto auf Pflaster |
0.04 |
Eisenbahn |
0.003 |
Tabelle 3: Rollreibungszahlen (Quelle: Dobrinski
et al, Lit [10])
Angenommen, das Erdreich sei "klebrig" und die Kombination Reifen-Erde
weist eine relativ "gute Haftung" von µ' = 0.7 auf, so gilt für die
Haftreibungskraft F_Haft für ein Rad:
F_Haft = µ' * F_g = 0.7 * 45N = 31.5N
Da im Gegensatz zum ersten Beispiel alle vier Räder betroffen sind,
ergibt sich für das gesamte, erforderliche Dremoment für alle vier Räder:
(2) M_Haft= 4 * F_Haft * r_Rad=
4*31.5N*0.078m= 9.82Nm
Auch bei diesem Beispiel gilt, dass das vom Antrieb aufzubauende
Drehmoment grösser sein muss, um das Fahrzeug aus dem Dreck bewegen zu
können.
|
3.2.3. Überfahren einer ebenen Fläche
|
Diese Berechnung sollte ein "Gefühl" dafür geben, welche Drehmomente
beim "normalen" Fahrbetrieb auf hartem Untergrund auftreten. Es soll
ersichtlich werden, in welchem Verhältnis dazu die zuvor berechneten Werte
für "Extremsituationen" gegenüber dem "Normalbetrieb" stehen.
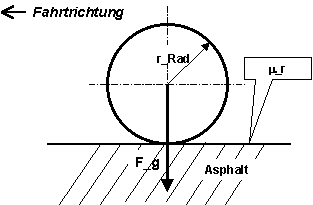
Bild 3: Überfahren einer ebenen Fläche
Beim Fahren auf hartem Untergrund (Bsp. Asphalt, Pflaster, etc.) ist
der Rollwiderstand (die sog. 'Rollreibung') zu überwinden, welche ein
Vielfaches kleiner ist, als die Haftreibung im vorigen Beispiel. Für die
Berechnung wird mit dem Gesamtgewicht des Fahrzeuges (18kg) gerechnet und
von obiger Tabelle die Rollreibungszahl µ_r = 0.04 (Auto auf Pflaster) verwendet:
F_Roll = F_g * µ = 180N * 0.04 = 7.2N
Für das benötigte Antriebsdrehmoment gilt:
(3) M_Roll = F_Roll * r_Rad = 7.2N *
0.078m = 0.56Nm
Also rund 17-mal weniger, als beim Überfahren von feuchtem Erdreich.
Anders sieht es dagegen aus, wenn man eine Steigung befährt. Da lassen bei
einigen Modellen schon mal die Kräfte nach. Damit das nicht passiert,
schätzt man die Drehmomente besser vorgängig ab wie
folgt:
|
3.2.4. Überfahren einer Steigung
|
Um
mit dem Fahrzeug auch eine Steigung überwinden zu können, muss zusätzlich
zur Überwindung dieser Rollwiderstandskraft noch das
Fahrzeuggewicht mit einbezogen werden. Dieses wirkt
umso mehr, je steiler der Winkel der Steigung zur horizontalen Ebene ist.
Bild 4: Überfahren einer Steigung
Bei einem Winkel von 45° (100% Steigung), wirkt die Gewichtskraft mit
einem Anteil F_g' von::
F_g' = sin(α) * F_g = cos(45°) * 180N =
127N
Auch beim Überfahren einer Steigung wirkt eine Rollwiderstandskraft
F_g'' senkrecht zur Unterlage wie folgt: F_g''(wirksam beim
Rollwiderstand):
F_g'' = cos(α) * F_g = sin(45°) * 180N =
127N
Für das gesamthaft benötigte Antriebsdrehmoment müssen beide Kräfte
F_g' und F_g'' wie folgt berücksichtigt werden. Als Rollreibungszahl wird
wieder µ_r = 0.04 angenommen.
(4) M_Steigung = M_g' +
M_Roll_F_g''=
(F_g' * r_Rad) + (F_g'' * µ_r * r_Rad) =
(127N * 0.078m) +
(127N * 0.04 * 0.078m) = 10.3Nm
|
3.2.5. Zusammenfassung der Ergebniss nach der "Drehmomentmethode":
|
Die vorangegangenen Drehmomentberechnungen zeigen auf, in welchen Fahrsituationen etwa welches Drehmoment an den
Radabtrieben benötigt wird. Damit nun das Modellfahrzeug die gewünschten Fahrsituationen meistern kann,
muss das an den Radabtrieben benötigte Drehmoment vom EMotor "geliefert"
werden. Nachfolgend nochmals die zusammengefassten Ergebnisse:
Fahrsituation |
Drehmoment [Ncm] ohne mech. Verluste |
Überfahren einer Schwelle |
3.06 |
Überfahren von feuchtem Erdreich |
9.82 |
Überfahren einer ebenen Fläche |
0.56 |
Überfahren einer Steigung |
10.3 |
Tabelle 3: Benötigtes Drehmoment nach Drehmomentmethode am Radabtrieb
Das höchste, aufzubringende Antriebsdrehmoment am Radabtrieb (nicht am EMotor-Abtrieb!) ist
in der Grössenordnung von M = 10Nm anzusiedeln (45°-Steigung,
Erdreich). Es finden sich wohl keine EMotoren, welche derartige
Drehmomente erzeugen können und zudem noch ins geplante Modellfahrzeug
passen. Abhilfe schafft ein Getriebe, welches die Drehzahl des EMotor-Abtriebs reduziert
und dessen Drehmoment zum Radabtrieb hin erhöht.
Bei diesen Berechnungen nach der "Drehmomentmethode" sind noch keine mechanischen
Verluste eingerechnet, welche sich beispielsweise durch die verwendete Lagerung der Antriebswellen (Bsp. Kugellager, Buchsen)
und die Zahnradpaarungen (Getriebestufen, Differntiale) ergeben. Diese mechanischen Verluste müssen
zusätzlich vom Antriebsmotor "überwunden" werden.
Für die angestellten Berechnungen nach der "Massstabsmethode" bedeutet dies, dass noch
ein zusätzliches Drehmoment zu dem vorgängig berechneten Antriebsdrehmoment - in meinem Fall M=10Nm -
zur Überwindung der mechanischen Verluste addiert werden muss. Diese Abschätzung folgt im nachfolgenden Abschnitt.
|
3.2.6. Abschätzung der mechanischen Verluste
|
HINWEIS:
Nachfolgende Ergebnisse sind nach (!) Berechnung der Getriebe-Übersetzungen erneut nachzurechnen, da erst dann die genaue Anzahl Zahnradpaarungen bekannt sind.
|
Da man an dieser Stelle noch nicht weiss, welche und wieviele Übersetzungsstufen das zukünftige Modellgetriebe haben wird, kann man einen Faktor "Handgelenk mal Pi"
verwenden.
Man kann wohl davon ausgehen, dass die Achsen mehrfach untersetzt sind (bei Kaufteilen sind die Anzahl der Untersetzungsstufen sowie die Übersetzungsverhältnisse vorgegeben) und
es ist nicht falsch, davon auszugehen, dass das zum Einsatz kommende Getriebe über mindestens 4 Zahnradpaarungen verfügt.
Ich halte es für angebracht, von einem schlechteren Wirkungsgrad auszugehen, als umgekehrt - also ein wenig mehr Leistung an Bord zu haben als zu wenig.
Die mechanischen Verluste einer Zahnradpaarung sind in zahlreichen Fachliteraturen nachzulesen. Ich ging in meiner Berechung von den
Angaben von T.Wallroth [Lit.1] aus, welcher besagt, dass der Verlustfaktor [η_x] pro Stirnradpaarung mit 0.9, derjenige von
Kegelradpaarungen mit 0.8 anzunehmen ist. Maschinenbau-Fachartikel
erwähnen oft einen Verlustfaktor von 2% pro Stirnradpaarung. Als "goldenen
Mittelweg" nehme ich 5% an, was einem Verlusfaktor von 0.95 entspricht.
Plant man nun ein allradgetriebenes Modellfahrzeug mit zwei Portalachsen wie bei einem Unimog, so ergeben sich als Schätzung
für den kompletten Antriebsstrang (EMotor - Radabtrieb) folgende, mechanischen Verluste:
- 8 Stirnradpaarungen (1 x E-Motor, 2 x Getriebe, 1 x Zentraldifferential, 4 x Radvorgelege der Portalachsen)
- 2 Kegelradpaarungen (2 x Kegel-Telleradkombinationen bei Achsdifferentialen)
Die bei Kurvenfahrt oder Schlupf auftretenden internen Verluste der Differentialgetriebe, kann man zur Vereinfachung erstmal vernachlässigen.
Somit lassen sich die mechanischen Verluste wie folgt abschätzen:
η_Antrieb = (0.95)^8 * 0.8^2=
0,66 * 0.64 = 0.42
Der geschätze Wirkungsgrad des Antriebsstranges bedeutet, dass
58% der zugeführten Energie nutzlos im
Antriebsstrang "verpuffen". Die Bilanz sieht noch schlechter aus, wenn der
Wirkungsgrad des verwendeten Elektromotors mit einbezogen wird. Geht man davon aus, dass dieser über 70% betragen muss, ergibt
sich ein geschätzter Gesamtwirkungsgrad des kompletten Antriebstranges von:
η_tot_Antrieb = η_Antrieb * η_EMot = 0.42 *
0.70 = 0.29
Es kann also davon ausgegangen werden, dass etwa 70% der vom EMotor abgegebenen Leistung im Antriebsstrang verpuffen.
Um das geforderte Drehmoment am Radabtrieb dieses Antriebsstranges zu erreichen, muss der EMotor also ein um den Faktor 3.3 höheres Drehmoment abgeben (100/30=3.3).
|
Beispiel Unimog-Modell:
Nachdem die Getriebeplanung abgeschlossen war, konnte die Neuberechnung der möglichen, mechanischen Verluste
abschliessend durchgeführt werden. Mein Getriebeplanung sah den Einsatz eines Dreiganggetriebes mit nachgeschalteter Reduktionsstufe vor (Vergleiche Kapitel 'GETRIEBEPLANUNG').
Der komplette, geplante Antriebstrang inklusive 6-gang-Getriebe weist 11 Stirnradpaarungen
(1 x E-Mot. - 3 x Hauptgetriebe - 2 x Gruppenschaltung - 1 x
Zentraldifferential - 4 x Radvorgelege) sowie zwei Kegelradpaarungen (2 x
Kegel -Telleradkombinationen bei Achsdifferentialen) auf.
Die möglichen, auftretenden Verluste
schätzen sich ab zu:
η_Antrieb = (0.95)^11 * 0.8^2=
0,57 * 0.64 = 0.365
Eine Anforderungen
meinerseits war, dass dieser über 85% betragen muss, respektive innerhalb des optimalen Wirkungsgrades betrieben werden sollte. Es ergibt
sich somit ein geschätzter Gesamtwirkungsgrad des kompletten Unimog-Antriebs
von:
η_tot_Antrieb = η_Antrieb * η_EMot = 0.365 *
0.85 = 0.31
Bei meinem zukünftigen Modell ging ich also davin aus, dass schätzungsweise 70% der zugeführten, mechanischen Leistung wirkungslos in Form von mechanischen Verlusten im Antriebsstrang verpuffen.
|
3.2.7. Bestimmung des minimal benötigten Übersetzungsverhältnisses zur Erreichung des maximal benötigten Drehmoments
|
Dieses Unterkapitel dient dazu, die grösste Übersetzung des Modellgetriebes zu bestimmen, welche dann Basis ist für die Getriebeplanung. Diese ist direkt davon abhängig,
welcher EMotor eingesetzt wird - also dessen Lastdrehmoment und dessen Lastdrehzahl. Um sich schrittweise an das Ergebnis heranzutasten, können auch Nenndrehmomente und Nenndrehzahlen verwendet werden, welche meist in den Datenblättern der Herstellern direkt abgelesen werden können.
Ob diese minimal benötigte Übersetzung schlussendlich dem kleinsten Gang entsprechen soll, oder ob das maximale Drehmoment am Radabtrieb auch in höheren Gangstufen erreicht werden soll, ist eine persönliche Entscheidung. Das höchste Drehmoment sollte beispielweise bei einem
Traktor in einem breiten Einsatzgebiet zur Verfügung stehen (Bsp. Gang 1 und 2) und bei einem LKW vielleicht nur im kleinsten Gang (1.Gang).
Höchstwahrscheinlich hat man bereits ein paar EMotor-Typen von unterschiedlichen
Herstellern in die nährere Auswahl bezogen. Kriterien waren vielleicht Preis, Grösse, Ideen aus Internetforen oder Modellbaukollegen.
Es gilt nun, für diesen EMotor, respektive diese EMotoren die benötigten Übersetzungsverhältnisse zu bestimmen, um vorgängig bestimmte, maximal benötigte Antriebsdrehmoment zu erreichen.
Mit den nachfolgenden, einfachen Berechnungen auf Basis eines oder mehreren EMotoren bekommt man einen Eindruck der notwendigen Untersetzungen und kann auf Grund
des Ergebnisses / der Ergebnisse entscheiden, ob ein EMotor mit geringerem oder höherem Drehmoment eingesetzt werden sollte.
Beispiel: Man erhält als Resultat eine notwendige Untersetzung von i = 760. Eine so hohe Untersetzung dürfte schwer machbar sein, respektive nur mittels einer Vielzahl von Untersetzungsstufen, was man eigentlich vermeiden will (Verluste, Platz, Aufwand zur Herstellung, Kosten). Ergo wählt man einen EMotor mit vielleicht doppeltem (Nenn-)Drehmoment aus und rechnet erneut.
Ist das Ergebniss im Bereich zwischen i = 100 und i = 200, so kann man davon ausgehen, dass diese Untersetzungen in einem herstellbaren Bereich liegen.
Für die Bestimmung der maximal benötigten Getriebeuntersetzung verwendet man also das (Nenn-)Drehmoment des EMotors (Herstellerangaben) und die zuvor berechneten
Werte für das benötigte, maximale Drehmoment und den Gesamtwirkungsgrad wie folgt:
i_max_Antrieb = M_theor / (η_tot_Antrieb * M_Nenn_EMot)
Am Beispiel von drei EMotoren mit Nenndrehmomenten von a) 30Ncm, b) 10Ncm und d) 5Ncm ergeben sich folgende Gesamtübersetzungen:
a) i_max_Antrieb = 10Nm / (0.31 * 0.30Nm) = 107
b) i_max_Antrieb = 10Nm / (0.31 * 0.10Nm) = 322
c) i_max_Antrieb = 10Nm / (0.31 * 0.05Nm) = 645
Ein EMotor mit einem Nenndrehmoment von 30Ncm müsste also mit einem Getriebe mit einer Untersetzung von i=107 an seinem Abtrieb ausgestattet werden,
um das benötigte Antriebsdrehmoment von M = 10Nm zu erzeugen und die Verluste im Antriebsstrang zu "kompensieren". Man erkennt bei diesem Schritt auch, dass
eine Übersetzung von i = 645 nur mit einer Vielzahl von Übersetzungsstufen (oder einem Schneckengetriebe, welches hohe mechanische Verluste hat) erreicht werden kann und aus diesem Grund ausscheidet.
Je höher die Getriebeuntersetzung und je höher die (Nenn)Drehzahl
des EMotors gewählt wird, desto kleiner muss das benötigte (Nenn)Drehmoment
des EMotors sein.
Die vorangegangenen Drehmomentberechnungen stellen sicher, dass genügend Kraft an den Radabtrieben aufgebaut wird um die gewünschten Fahrsituationen (Überfahren von Schwelle, Steigung, etc.) meistern zu können,
jedoch weiss man nicht, ob mit dieser Untersetzung und dem gewählten EMotor auch die zu Beginn bestimmten Wunschgeschwindigkeit(en) erreicht werden können.
Hierfür nutzt man lediglich den Raddurchmesser (Aussendurchmessser Reifen) kennen um die Raddrehzahl bei der gewünschten Geschwindigkeit zu bestimmen. Anschliessend dividiert man die Drehzahl des EMotors mir dieser Raddrehzahl und erhält das notwendige Übersetzungsverhältnis.
Die Raddrehzahl 'n_Rad' bei einer Geschwindigkeit x errechnet sich zu:
n_Rad = Geschwindigkeit / Radumfang =
v_x / (d_Rad * PI * 3.6)
Die Übersetzung 'i' bei einer Geschwindigkeit x errechnet sich zu:
i_x.Gang = n_EMot / n_Rad_x.Gang
Anschliessend lässt sich das minimal benötigte Drehmoment des EMotors bestimmen, indem das vorgängig bestimmte maximale Drehmoment mit der errechneten Übersetzung dividiert wird (das getriebe multipliziert
quasi das vom EMotor abgegebene Drehmoment, ohne jedoch den ebenfalls errechneten Verlustfaktor zu vergessen und zwar wie folgt:
M_Emot_x = M_max / (η_tot_Antrieb * i_x.Gang)
Somit erhält man das minimal benötigte Drehmoment des einzusetzenden EMotors und zwar an dessen Abtrieb.
|
Beispiel Unimog-Modell:
Das maximale Drehmoment am Radabtrieb von M_max=10Nm muss nur auf jeden Fall im kleinsten Gang, kann jedoch auch im zweiten Gang anliegen. Die geringste Soll-Geschwindigkeit im 1.Gang soll 0.05m/s und diejenige im 2.Gang 0.3 m/s betragen.
Bei 156mm Reifendurchmesser ergibt sich für die Raddrehzahl bei diesen beiden Geschwindigkeiten:
n_Rad_1.Gang = 0.05 m/s * 60s / (0.156m * 3.14) = 6.2 1/min
n_Rad_2.Gang = 0.3 m/s * 60s / (0.156m * 3.14) = 36.7 1/min
Da die (Nenn-)Drehzahl des EMotors noch unbekannt ist, bietet sich eine Tabelle an, indem ein paar typische EMotor-Drehzahlen aufgelistet werden um zu jeder Drehzahl die Übersetzung zu bestimmen.
Geschwindigkeit = 0.05m/s |
Drehzahl EMotor [1/min] |
Übersetzung i [] |
Abgangs-Drehmoment EMotor [Ncm] |
Abgangs-Leistung EMotor [W] |
2000 |
322 |
10 |
20 |
3000 |
483 |
6.7 |
20 |
4000 |
645 |
5 |
20 |
5000 |
806 |
4 |
20 |
Geschwindigkeit = 0.3m/s |
Drehzahl EMotor [1/min] |
Übersetzung i [] |
Abgangs-Drehmoment EMotor [Ncm] |
Abgangs-Leistung EMotor [W] |
2000 |
54 |
59 |
118 |
3000 |
82 |
39.6 |
118 |
4000 |
109 |
29.6 |
118 |
5000 |
136 |
23.4 |
118 |
Tabelle 4: Mögliche EMotor-Abgangsdrehzahlen und -drehmomente
Ein Blick in die Datenblätter von EMotor-Herstellern lässt erkennen, dass EMotoren mit einem Nenndrehmomet im bereich von 10-15Ncm in etwa diejenigen Abmessungen aufweisen, wie im Modell nich unterzubringen ist. Im Bezug auf obiges Beispiel für den Unimog bededutet dies, dass bei der Wahl eines soclhen Emotors das
maximal benötigte Drehmoment am Radabtrieb von 10Nm nur im kleinsten Gang zur Verfügung stünde.
|
4. Variantenvergleich
|
4.1 Vergleich der Ergebnisse
|
Nachstehend eine Tabelle mit dem direkten Vergleich der beiden Variantenergebnisse am Beispiel meines Unimogs
|
|
Massstabsmethode |
Drehmomentmethode |
Drehzahl [1/min] |
Drehmoment [Ncm] |
Abgangs-Leistung [W] |
Drehmoment [Ncm] |
Abgangs-Leistung [W] |
|
|
|
von |
bis |
von |
bis |
2'000 |
36 |
72 |
10 |
59 |
20 |
118 |
3'000 |
24 |
72 |
6.7 |
39.6 |
20 |
118 |
4'000 |
18 |
72 |
5 |
29.6 |
20 |
118 |
5'000 |
14.4 |
72 |
4 |
23.4 |
20 |
118 |
Tabelle 5: Ergebnisvergleich der Varianten
|
4.2 Fazit
|
Die Massstabsmethode scheint ein gutes Instrument zu sein, auf einfachstem
Weg einen genügend dimensionierten Antriebsmotor
auszuwählen.
P_EMot_ab_Massstabsmethode = 72W
P_EMot_ab_Drehmomentmethode = 20W bis 118W
Die Berechnung nach der "Massstabsmethode" lässt jedoch gewisse
Zweifel bezüglich des Korrekturfaktors, respektive den erreichbaren Geschwindigkeiten offen. Diese
können mit der "Drehmomentmethode" besser beantwortet werden,
man bekommt quasi ein "Gefühl" dafür, welche Geschwindigkeiten in Abhängigkeit des Drehmomentes erreicht werden können.
Die Drehmomentmethode gibt einen Bereich vor, in welchem sich die benötigte Antriebsleistung bewegen sollte.
Mit einer korrekten Getriebeuntersetzung ("Drehmomentübersetzung") erreicht man, dass der Antrieb die Anforderungen an unterschiedliche Fahrsituationen erfüllen kann und zudem noch im optimalen Wirkungsbereich arbeitet (optimale Akkulaufzeiten).
Bei den Berechnungen sind unbedingt die Verlustfaktoren
aller am Antrieb beteiligten Komponenten (Achsen, Getriebe, Radvorgelege)
mit einzubeziehen.
Man sollte nicht vergessen, dass das berechnete Drehmoment,
respektive die berechnete mechanische Leistung am EMotor-Abtrieb
(!) zur Verfügung stehen muss. Einige Herstellerangaben beziehen
sich oft nur auf die vom EMotor aufgenommene, elektrische Leistung,
welche immer höher ist als die mechanische Antriebsleistung. Die Angaben einiger Distributoren sind schlicht falsch. Versuche deshlab immer, Datenblätter vom Hersteller (!) zu nutzen.
Die endgültige Wahl des EMotors sollte mit der Getriebeplanung
einhergehen. Erst nachdem sich herausstellt, dass die geplante Getriebekonstruktion
a) den Drehmomenten standhalten wird und b) die Grösse des
Getriebes noch ins Modell passt, sollte man zum Kauf eines EMotors schreiten.
(Doch erst eine Flasche Wein entkorken, zweimal darüber schlafen,
alles nochmals überdenken und stichprobenartig nachrechnen.)
|